課題解決事例
新型EVに似合う近未来的でスタイリッシュな内装を実現したい…
デザイン性・表面硬度・環境負荷低減などの課題を一挙に解決した新フィルム材とは
自動車内装部品加工メーカー G社 設計開発部
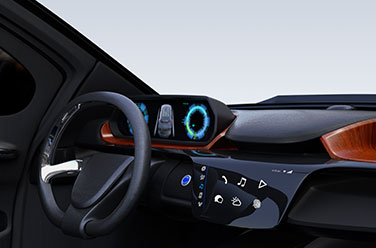
自動車部品メーカー経由で自動車メーカーから新型EV向け内装の開発を委託されたG社。自動車メーカーのデザイナーからは、近未来的な外観フォルムに合ったスマートな内装にしたいという強い要望があった。一方、資材部からは、エコ調達の方針に沿って部品製造工程での環境負荷を減らすよう要請があり、設計開発部はこれらの両立に頭を痛めていた。
課題
リアルなボタンではなく、光って浮かび上がる「光透過表示+静電スイッチ」にしたい…
G社が担当する部品は、エアコンなどを操作するボタンが集中するインパネ中央の重要部品でした。デザイナーからは、これらのボタンを従来の物理的でリアルな押しボタンやトグルスイッチではなく、スタイリッシュな形にしたいとリクエストされていました。
最新情報を収集する中、設計開発部の担当者は「光透過表示+静電スイッチ」が目的に適合すると判断します。G社では印刷フィルムのインサート成形性部品の量産実績があったため、今回はその印刷部分に光透過印刷を使い、さらに静電スイッチに対応することで実現できるだろうと見通しを立てていました。しかし試作の段階で、熱成形フィルムに問題が見つかったのです。
光透過表示では光が透過する部分(文字や記号)の位置精度が要求されるため、インサート成形前に行うフィルムの熱成形時に成形性が良いフィルムが必要でした。しかし表面硬度が高いフィルムは熱成形性が良くないという特性があり、今回のアイデアを実現するうえで最大の難関となってしまったのです。さらに、資材部からの“エコ調達の方針”という点も、部材の選定を難しくしていました。
開発スタッフたちは、従来とは別の製造工法を探す必要に追いやられました。
課題のポイント
- デザイナーの要望に応えるため「光透過表示+静電スイッチ」を採用したかったが、使用する熱成形フィルムに問題が発覚
- 実績のある熱成形フィルムを使った工法では、表面硬度と熱成形性が両立できない
- 資材部からの“エコ調達の方針”という点が、部材の選定をさらに難しくしていた
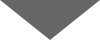